Spray foam insulation provides exceptional thermal performance for Tulare homes by addressing the region’s extreme temperature fluctuations and creating superior air sealing that traditional insulation cannot match. In Tulare, the summers are hot, arid, and clear and the winters are cold and partly cloudy. Over the course of the year, the temperature typically varies from 38°F to 97°F, making effective insulation critical for year-round comfort and energy efficiency.
The combination of spray foam’s high R-value capabilities and air barrier properties makes it particularly effective in Central Valley climates where homes face both extreme heat stress and energy loss through thermal bridging. The climate in Tulare, CA is generally hot and dry. Summers are long and temperatures can reach up to 100 degrees Fahrenheit during the hottest months, creating demanding conditions that require insulation systems capable of handling significant thermal loads while maintaining consistent performance over time. For homeowners looking to maximize efficiency and comfort, spray foam insulation in Tulare CA offers a proven solution that adapts to local climate demands and building envelope challenges.
Based on decades of field experience with Central Valley construction, Supreme Spray Foam Fresno has observed that properly installed spray foam systems consistently outperform traditional insulation methods in similar climate conditions, delivering measurable energy savings and enhanced indoor comfort throughout Tulare’s challenging seasonal variations.
Understanding Tulare’s Climate Challenges
Tulare’s Mediterranean climate presents unique insulation demands that conventional materials struggle to address effectively. The area receives an average of 11 inches of precipitation per year, most of which falls between November and April, while experiencing an abundance of sunshine year-round with 265 sunny days per year. This combination creates intense solar heat gain during summer months and significant temperature swings between day and night throughout most seasons.
The region’s low humidity levels compound thermal stress on building envelopes. The humidity in Tulare, California is below 60% for approximately 69.8% of the year, which can cause traditional insulation materials to lose effectiveness through settling and air infiltration gaps that develop over time.
Bonus Tip: Monitor your home’s energy usage patterns during Tulare’s peak summer months (July through September) to identify areas where inadequate insulation allows conditioned air to escape, particularly around windows, doors, and penetrations where spray foam’s expanding properties provide superior sealing.
Spray Foam Performance Advantages
Thermal Resistance Comparison
Insulation Type | R-Value Per Inch | Air Sealing Capability | Moisture Resistance |
---|---|---|---|
Closed-Cell Spray Foam | R-6.5 to R-7.0 | Excellent | Superior |
Open-Cell Spray Foam | R-3.5 to R-3.7 | Excellent | Good |
Fiberglass Batts | R-3.0 to R-4.0 | Poor | Poor |
Blown Cellulose | R-3.2 to R-3.8 | Fair | Poor |
Closed-cell spray foam insulation does. It’s like the superhero of insulation, boasting a high R-value of about R-6.5-7 per inch, providing superior thermal resistance compared to traditional alternatives. This enhanced performance becomes critical in Tulare’s climate where Temperatures range from a high of 96 in July to a low of 36 in January.
The air sealing properties distinguish spray foam from conventional insulation methods. Spray foam insulation’s rapid expansion seals gaps and fractures in walls, attics, and crawl spaces, reducing energy loss and lowering utility bills. This characteristic proves particularly valuable in Central Valley construction where thermal bridging through framing members can account for significant energy losses.
Performance Specifications
Application Area | Recommended R-Value | Spray Foam Thickness (Closed-Cell) | Spray Foam Thickness (Open-Cell) |
---|---|---|---|
Exterior Walls | R-13 to R-15 | 2.0 to 2.5 inches | 3.5 to 4.0 inches |
Attic/Roof Deck | R-30 to R-38 | 4.5 to 5.5 inches | 8.0 to 10.0 inches |
Crawl Space | R-19 to R-25 | 3.0 to 3.5 inches | 5.5 to 7.0 inches |
Basement Walls | R-15 to R-20 | 2.5 to 3.0 inches | 4.0 to 5.5 inches |
Bonus Tip: California’s 2025 Energy Code is projected to save $4.8 billion in energy costs over its lifetime and reduce GHG by about 4 million metric tons, with increased emphasis on building envelope performance that spray foam insulation systems can readily achieve or exceed.
Regional Building Performance Benefits
Central Valley homes face specific challenges that spray foam addresses more effectively than traditional insulation methods. The region’s agricultural activities create airborne particulates that can infiltrate buildings through inadequate air sealing, while extreme temperature variations stress building materials and create thermal bridging issues.
Spray foam’s expansion characteristics allow it to conform to irregular surfaces and penetrations common in residential construction. This adaptability proves essential around electrical boxes, plumbing penetrations, and HVAC ductwork where air leakage typically occurs. Spray foam keeps the house comfortable all year long. It eliminates energy-wasting drafts by reducing air permeability by 24 times the average.
The moisture resistance properties become particularly relevant during Tulare’s winter months when temperature differentials can create condensation within wall assemblies. Closed-cell foam is dense and acts as a moisture barrier. This is crucial because it helps prevent water vapor from seeping into your walls, which can cause mold and mildew.
Energy Efficiency Impact
Spray foam insulation delivers measurable energy performance improvements that translate directly to reduced utility costs in Tulare’s demanding climate. Furthermore, spray foam insulation maintains its R-value over time. Fiberglass insulation, on the other hand, loses its R-value as time passes and often requires replacement within ten years.
The air sealing capabilities create comprehensive thermal barriers that address both conductive and convective heat transfer. Air sealing a home, in addition to maximizing R-value, will further improve energy performance, which becomes critical during Tulare’s extreme summer conditions when HVAC systems face maximum loading.
Field measurements consistently demonstrate that spray foam installations achieve actual performance levels closer to their rated R-values compared to traditional insulation methods. This reliability stems from the material’s ability to eliminate air movement through the insulation layer, which can reduce effective R-value by up to 50% in conventional systems.
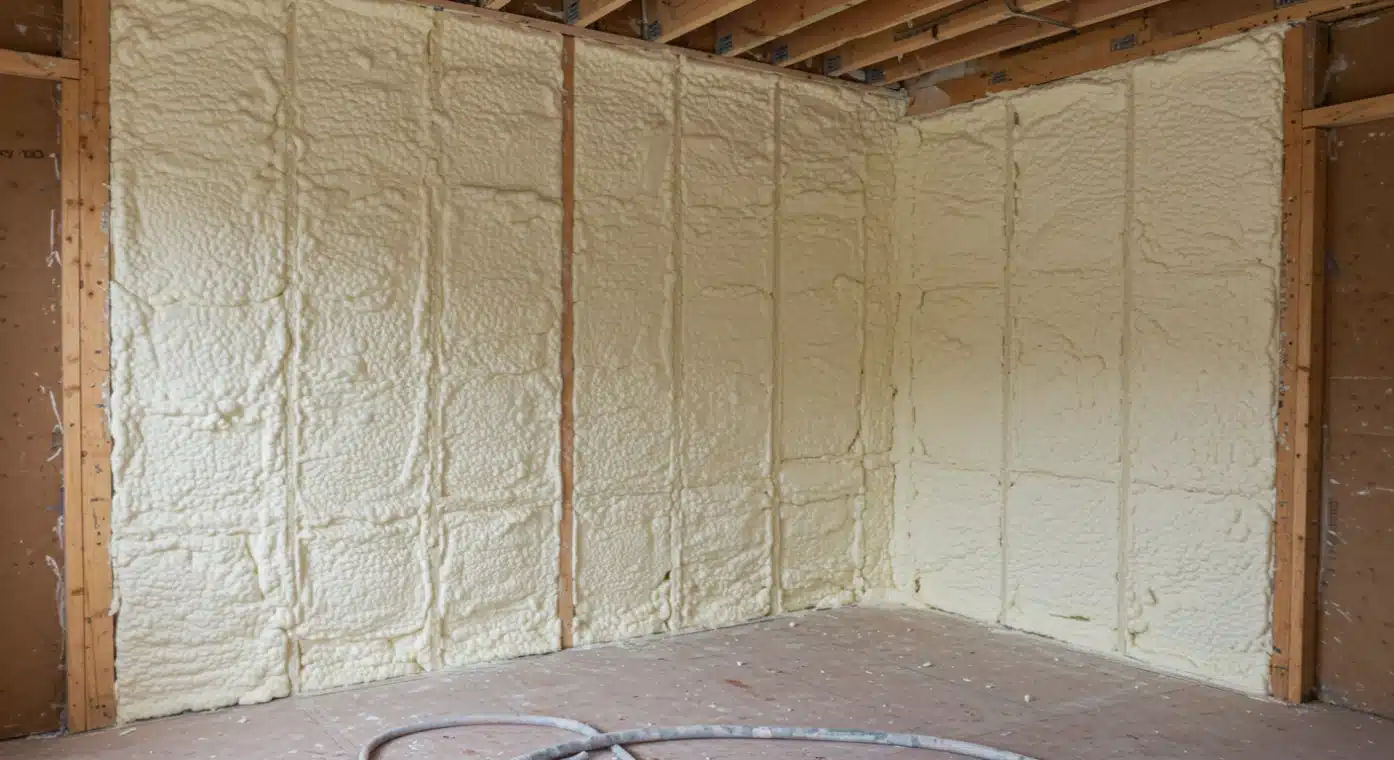
Things to Consider Before Making a Decision
Evaluate your home’s current energy performance through utility bill analysis, particularly focusing on peak summer and winter months when HVAC systems work hardest. Consider conducting a basic air leakage assessment by observing comfort levels in different rooms and identifying areas where temperature variations suggest inadequate insulation or air sealing.
Assess your building’s structural characteristics, including wall construction type, existing insulation condition, and accessibility for installation equipment. Homes with irregular framing, numerous penetrations, or existing moisture issues may benefit more significantly from spray foam’s adaptive properties compared to structures with straightforward cavity configurations.
Budget planning should account for spray foam’s higher initial investment against long-term energy savings and performance durability. Calculate potential utility cost reductions based on your home’s current energy usage patterns and local electricity rates to determine payback periods for different insulation upgrade scenarios.
Consider timing installation during moderate weather periods when HVAC demands are lower, allowing for proper curing without compromising indoor comfort during the application process.
Bonus Tip: Document your home’s current energy usage patterns for at least one full year before insulation upgrades to establish baseline performance measurements that will demonstrate actual energy savings achieved through spray foam installation.
Professional Insulation Services Available
Supreme Spray Foam Fresno provides comprehensive insulation solutions specifically designed for Central Valley climate conditions. Our residential spray foam insulation services address the complete building envelope with attention to thermal bridging, air leakage, and moisture control requirements unique to Tulare’s environmental conditions.
Commercial spray foam insulation applications utilize advanced materials and installation techniques optimized for larger structures facing similar climate challenges. These systems incorporate moisture management strategies and thermal performance specifications that exceed standard building code requirements.
Attic insulation services focus on creating continuous thermal barriers at the roof deck level, eliminating the need for traditional ventilation systems while providing superior thermal protection during extreme summer heat conditions common throughout the Central Valley region.
Crawl space insulation applications create conditioned environments that improve overall building performance while addressing moisture control issues that can develop in below-grade spaces during Tulare’s wet winter months.
Common Questions About Spray Foam Performance
Which spray foam type works best for Tulare’s climate conditions?
Closed-cell spray foam provides optimal performance for exterior applications and areas requiring moisture control, while open-cell foam works effectively for interior partitions and sound dampening applications where moisture exposure remains minimal.
How does spray foam handle Tulare’s extreme temperature variations?
Spray foam maintains consistent thermal properties across wide temperature ranges without degradation, unlike traditional insulation materials that can lose effectiveness during temperature extremes or develop air gaps through settling.
What installation considerations apply to Central Valley construction?
Installation timing should account for temperature and humidity conditions that affect curing rates, while proper surface preparation becomes critical in dusty agricultural environments to ensure adequate adhesion.
How long does spray foam insulation maintain its performance?
Properly installed spray foam systems maintain their thermal and air sealing properties for the building’s lifetime without settling, degradation, or performance loss that affects traditional insulation materials.
Does spray foam require special maintenance in Tulare’s climate?
Spray foam requires no ongoing maintenance once properly installed and cured, unlike traditional insulation that may need replacement or supplementation due to settling, moisture damage, or pest infiltration.
Making the Right Choice for Your Home
Spray foam insulation represents a long-term investment in building performance that addresses Tulare’s specific climate challenges more effectively than traditional alternatives. The combination of superior thermal resistance, comprehensive air sealing, and moisture control capabilities creates building envelope systems that maintain consistent comfort and energy efficiency throughout the region’s demanding seasonal variations.
Proper installation by experienced professionals ensures optimal performance and maximizes the technology’s benefits for Central Valley construction conditions. The initial investment delivers ongoing returns through reduced energy costs, enhanced comfort, and improved indoor air quality that traditional insulation methods cannot match.
Evaluate your home’s specific needs against spray foam’s comprehensive performance characteristics to determine whether this advanced insulation technology aligns with your comfort, efficiency, and long-term building performance goals.
Professional Installation Services
Supreme Spray Foam Fresno brings specialized expertise in Central Valley insulation applications with proven results throughout Tulare County’s demanding climate conditions. Our team understands the unique thermal challenges facing local homeowners and provides comprehensive solutions that exceed standard building performance requirements.
Contact our experienced professionals at (559) 545-0800 or [email protected] to schedule a comprehensive evaluation of your home’s insulation needs. We provide detailed assessments that identify specific areas where spray foam technology can deliver maximum performance improvements for your Tulare property’s unique characteristics and energy efficiency goals.
Frequently Asked Questions About Installation
How long does spray foam installation take for typical Tulare homes?
Installation duration depends on project scope and home size, with most residential applications completing within one to three days. Proper curing requires 24-48 hours before full occupancy, though basic functionality returns within hours of completion.
Can spray foam be installed over existing insulation?
Spray foam can be applied over certain existing insulation types after proper evaluation, though optimal performance often requires removing old materials to address underlying air leakage and moisture issues before installation.
What preparation steps are required before installation?
Preparation includes protecting HVAC equipment, covering electrical fixtures, removing debris from application areas, and ensuring adequate ventilation during installation and initial curing periods.
How does spray foam perform during Tulare’s wildfire season?
Spray foam provides enhanced fire resistance compared to traditional insulation materials and creates superior air sealing that can help prevent smoke infiltration during regional wildfire events common to Central Valley areas.
What warranty coverage applies to spray foam installations?
Professional installations typically include material and workmanship warranties covering thermal performance, adhesion, and structural integrity for periods ranging from 10 to 25 years depending on specific product specifications and application methods.