Spray foam insulation repairs become the preferred option when damage affects less than 30% of the total coverage area and the underlying substrate remains structurally sound. Minor issues like small gaps, surface cracks, or localized shrinkage typically require targeted repairs rather than complete replacement, preserving both performance and investment value.
The decision between repair and replacement depends on specific damage assessment criteria, age of installation, and performance expectations. Professional evaluation determines whether isolated problems warrant spot treatments or indicate systemic issues requiring comprehensive solutions. Understanding these factors helps property owners make informed decisions that maximize insulation effectiveness while minimizing unnecessary expenses.
Years of field experience with spray foam installations across various climate conditions have revealed consistent patterns in damage types and optimal repair strategies. This comprehensive analysis provides practical guidance based on real-world performance data and industry best practices.
Damage Assessment Criteria
Evaluating spray foam condition requires systematic inspection of multiple factors that influence repair viability. Surface-level damage often masks underlying issues, making thorough assessment essential before determining the appropriate intervention strategy.
Visual inspection reveals obvious problems like cracking, separation, or discoloration, but comprehensive evaluation includes moisture testing, thermal imaging, and structural integrity checks. These diagnostic tools identify hidden defects that could compromise repair effectiveness if left unaddressed.
Bonus Tip: Use infrared thermography during temperature differential periods to identify thermal bridging that indicates insulation gaps invisible to standard visual inspection.
Damage Type | Repair Threshold | Replacement Indicator |
---|---|---|
Surface cracks | Less than 1/4 inch wide | Multiple interconnected cracks |
Adhesion failure | Isolated areas under 2 sq ft | Widespread delamination |
Shrinkage gaps | Individual gaps under 1 inch | Systematic shrinkage pattern |
Moisture damage | Localized staining | Persistent moisture infiltration |
Thermal bridging | Spot thermal losses | Continuous thermal bypasses |
Age and Performance Factors
Installation age significantly influences repair effectiveness and long-term performance expectations. Spray foam systems typically maintain optimal performance for 20-30 years when properly installed and maintained, but environmental factors can accelerate degradation in specific areas.
Newer installations (under 5 years) with isolated damage usually respond well to repair techniques, as the existing foam maintains good adhesion properties and chemical compatibility with repair materials. Older systems may require more extensive evaluation to ensure repair materials bond effectively with aged foam.
According to the North American Insulation Manufacturers Association, properly maintained spray foam insulation retains 95% of its initial R-value after 10 years of service, making repairs economically attractive for systems within this performance window.
Technical Specifications for Repair Decisions
Understanding foam characteristics and performance metrics guides appropriate repair strategies. Different foam types exhibit varying repair compatibility and longevity expectations that influence decision-making processes.
Foam Type | R-Value per Inch | Typical Repair Life | Adhesion Strength |
---|---|---|---|
Open Cell | 3.5-3.8 | 8-12 years | 15-25 psi |
Closed Cell | 6.0-6.5 | 15-20 years | 25-40 psi |
High-Density Closed Cell | 6.5-7.0 | 20-25 years | 40-60 psi |
Environmental conditions affect repair material performance and compatibility. Temperature extremes, humidity fluctuations, and chemical exposure influence how repair materials integrate with existing foam systems.
Bonus Tip: Schedule repairs during moderate weather conditions (50-80°F, low humidity) to ensure optimal chemical curing and adhesion between new and existing foam materials.
Cost-Benefit Analysis Framework
Economic evaluation compares repair costs against replacement expenses while considering long-term performance implications. Simple cost comparison often overlooks factors like installation disruption, temporary climate control, and potential structural modifications required for complete replacement.
Repair projects typically cost 20-40% of full replacement expenses when addressing localized damage. However, extensive repairs approaching 50% of replacement costs may indicate underlying problems that warrant comprehensive solutions rather than temporary fixes.
Market data from the Spray Foam Alliance indicates that strategic repairs can extend system life by 5-10 years, providing substantial return on investment when properly executed. This performance extension often justifies repair costs even when approaching higher percentage thresholds.
Things to Consider Before Making a Decision
Several critical factors influence repair versus replacement outcomes beyond simple damage assessment. These considerations help property owners evaluate long-term implications and make decisions aligned with their specific circumstances.
Building use patterns affect insulation performance requirements and repair durability expectations. High-traffic commercial spaces may require more robust solutions than residential applications, influencing the threshold for repair viability.
Future renovation plans impact repair investment wisdom. Properties scheduled for major renovations within 2-3 years may benefit from temporary repairs rather than comprehensive replacements that could be disturbed during construction activities.
Climate zone requirements influence insulation performance standards and repair material selection. Northern climates with extreme temperature variations may require higher-performance repair materials than moderate climate zones.
Insurance coverage and warranty implications affect decision-making processes. Some repair methods may void existing warranties or complicate insurance claims, making professional consultation essential before proceeding.
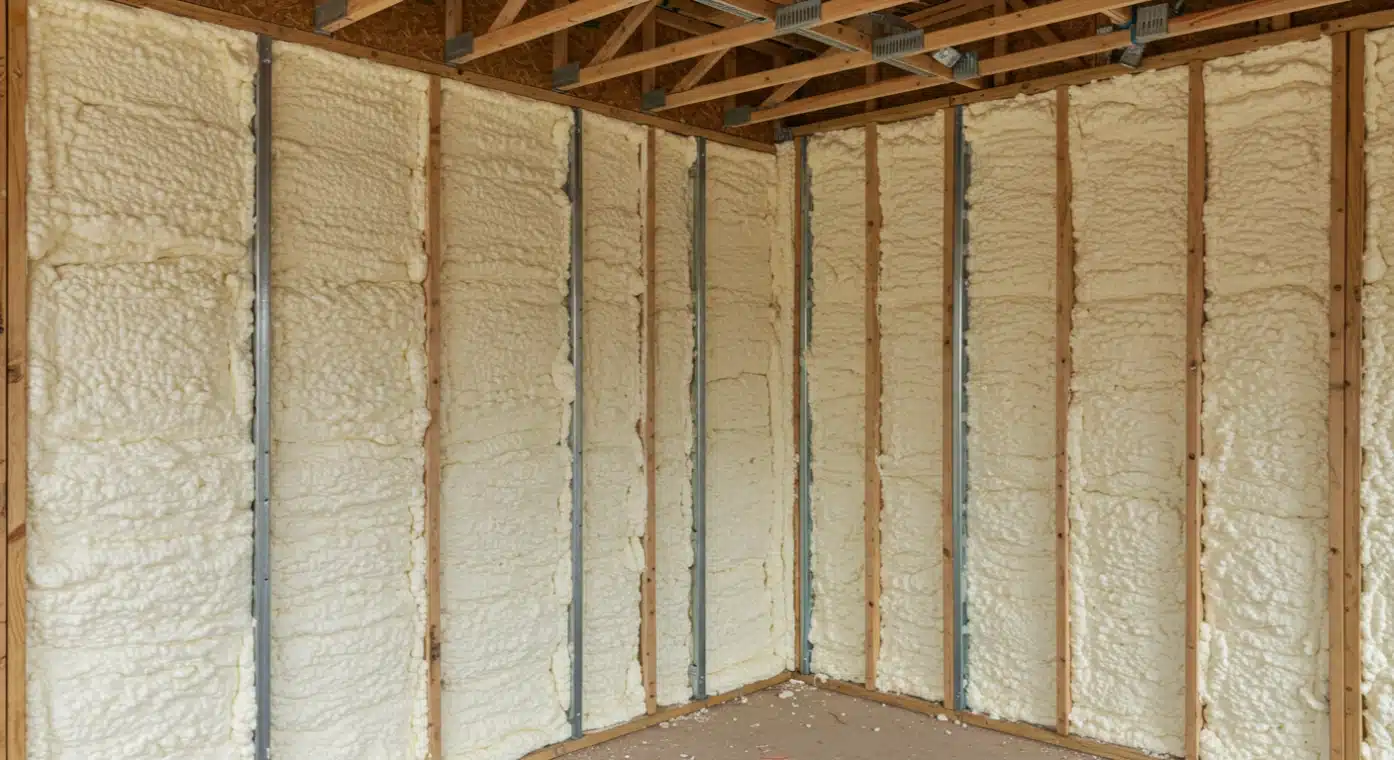
Supreme Spray Foam Fresno Professional Services
Supreme Spray Foam Fresno provides comprehensive insulation solutions tailored to specific property requirements and performance objectives.
- Spray Foam Repairs: Targeted interventions for isolated damage areas using compatible materials and proven application techniques that restore optimal thermal performance.
- Residential Spray Foam Insulation: Complete home insulation systems designed for maximum energy efficiency and comfort enhancement throughout all climate conditions.
- Commercial Building Spray Foam Insulation: Large-scale commercial applications with specialized equipment and materials meeting stringent performance standards and building codes.
- Attic Insulation: Comprehensive attic sealing and insulation services that address both thermal performance and air leakage control for optimal energy efficiency.
Key Takeaways for Spray Foam Repair Decisions
Successful spray foam repair decisions require comprehensive damage assessment, performance evaluation, and cost-benefit analysis tailored to specific property conditions. Minor damage affecting less than 30% of coverage area with structurally sound substrate typically warrants repair rather than replacement.
Professional evaluation provides accurate damage assessment and repair recommendations based on foam type, environmental conditions, and performance requirements. This expertise ensures repair investments deliver expected performance and longevity outcomes.
Strategic repairs can extend insulation system life by 5-10 years while maintaining optimal thermal performance. Property owners should evaluate their specific circumstances, including building use patterns, future renovation plans, and climate requirements, when making repair versus replacement decisions.
Professional Consultation and Service
Expert evaluation determines the most appropriate solution for your specific insulation challenges. Professional assessment considers all relevant factors including damage extent, system age, performance requirements, and long-term property goals.
Supreme Spray Foam Fresno brings extensive experience in spray foam evaluation and repair strategies across residential and commercial applications. Contact our team at (559) 545-0800 or [email protected] to schedule a comprehensive assessment and receive personalized recommendations for your insulation needs.
Common Questions About Repair Decisions
How long do spray foam repairs typically last?
Professional spray foam repairs using compatible materials typically last 8-15 years depending on environmental conditions and application quality. Proper surface preparation and material selection significantly influence repair longevity.
Can different foam types be used for repairs?
Repair materials must be chemically compatible with existing foam systems. Mixing incompatible foam types can result in poor adhesion, reduced performance, or accelerated degradation of both materials.
What environmental conditions affect repair success?
Temperature, humidity, and air movement during application significantly impact repair quality. Optimal conditions include temperatures between 50-80°F, relative humidity below 85%, and minimal air movement during curing.
Should repairs be performed by professionals or DIY?
Professional installation ensures proper surface preparation, material compatibility, and application techniques that maximize repair effectiveness. DIY repairs often fail due to inadequate preparation or inappropriate material selection.
How do repairs affect overall system performance?
Properly executed repairs restore localized thermal performance without compromising adjacent areas. Poor repairs can create thermal bridges or moisture infiltration points that reduce overall system efficiency.