Spray foam insulation eliminates drafty home problems in Lemoore by creating an airtight seal that blocks unwanted air infiltration through gaps, cracks, and penetrations in building structures. This comprehensive solution addresses temperature inconsistencies, energy waste, and comfort issues that plague many Central Valley homes due to the region’s extreme temperature variations and older construction methods.
The effectiveness stems from spray foam’s ability to expand and conform to irregular surfaces, sealing areas that traditional insulation materials cannot reach. Supreme Spray Foam Fresno has observed that homes in Lemoore typically experience a 30-50% reduction in energy costs and complete elimination of uncomfortable drafts after proper spray foam installation.
Understanding Lemoore’s Unique Climate Challenges
Lemoore’s location in California’s Central Valley creates specific challenges for home comfort and energy efficiency. Summer temperatures frequently exceed 100°F while winter lows can drop below 35°F, creating substantial thermal stress on building envelopes. Traditional insulation materials often fail to maintain consistent indoor temperatures due to air leakage around penetrations, electrical outlets, and structural joints.
The region’s agricultural environment also contributes to dust infiltration through these same air leakage points. Fortunately, solutions like spray foam insulation in Lemoore can effectively address both thermal performance and air quality by sealing structural gaps and preventing external contaminants from entering living spaces.
Technical Performance Comparison
Insulation Type | Air Sealing Capability | R-Value per Inch | Moisture Resistance | Longevity |
---|---|---|---|---|
Closed Cell Spray Foam | Complete air barrier | 6.0-7.0 | Excellent | 50+ years |
Open Cell Spray Foam | Partial air sealing | 3.5-4.0 | Good | 30+ years |
Fiberglass Batts | No air sealing | 3.1-3.4 | Poor | 15-20 years |
Cellulose | Minimal air sealing | 3.6-3.8 | Fair | 20-30 years |
Spray Foam Application Methods for Draft Elimination
Closed cell spray foam provides the most comprehensive solution for eliminating drafts in Lemoore homes. The material expands to fill every gap and crack while creating a structural bond with building materials. This dual function addresses both thermal bridging and air infiltration simultaneously.
Open cell spray foam offers effective draft reduction at a lower material cost, making it suitable for attic applications and interior walls where moisture control is less critical. The material’s flexibility allows it to accommodate normal building movement without compromising the air seal.
Bonus Tip: Focus spray foam application on rim joists, electrical penetrations, and HVAC ductwork connections where air leakage typically occurs most severely in Central Valley homes.
Regional Application Strategies
Lemoore’s climate demands specific attention to thermal bridging through structural components. According to the California Energy Commission, homes in the Central Valley lose approximately 25-40% of their heating and cooling energy through air leakage, making comprehensive sealing essential for comfort and efficiency.
The region’s temperature extremes require materials that maintain performance across wide temperature ranges. Spray foam’s cellular structure provides consistent thermal resistance regardless of outdoor conditions, unlike traditional insulation materials that can lose effectiveness in extreme heat or cold.
Installation Process and Draft Elimination
Professional installation begins with identifying all air leakage points using thermal imaging and pressure testing equipment. Common problem areas in Lemoore homes include band boards, electrical boxes, plumbing penetrations, and connections between different building materials.
The application process involves controlled expansion of the foam material to ensure complete coverage without over-expansion that could cause structural stress. Proper installation requires specific temperature and humidity conditions to achieve optimal cellular structure and adhesion.
Bonus Tip: Schedule spray foam installation during moderate weather conditions (60-80°F) for optimal material performance and curing in Central Valley climate conditions.
Material Specifications and Performance Data
Property | Closed Cell Specification | Open Cell Specification |
---|---|---|
Density | 2.0-2.5 lbs/ft³ | 0.5-0.8 lbs/ft³ |
Permeability | 0.8-1.5 perms | 16+ perms |
Compressive Strength | 25-50 psi | 1-2 psi |
Expansion Ratio | 30:1 | 120:1 |
Application Temperature | 60-100°F | 60-90°F |
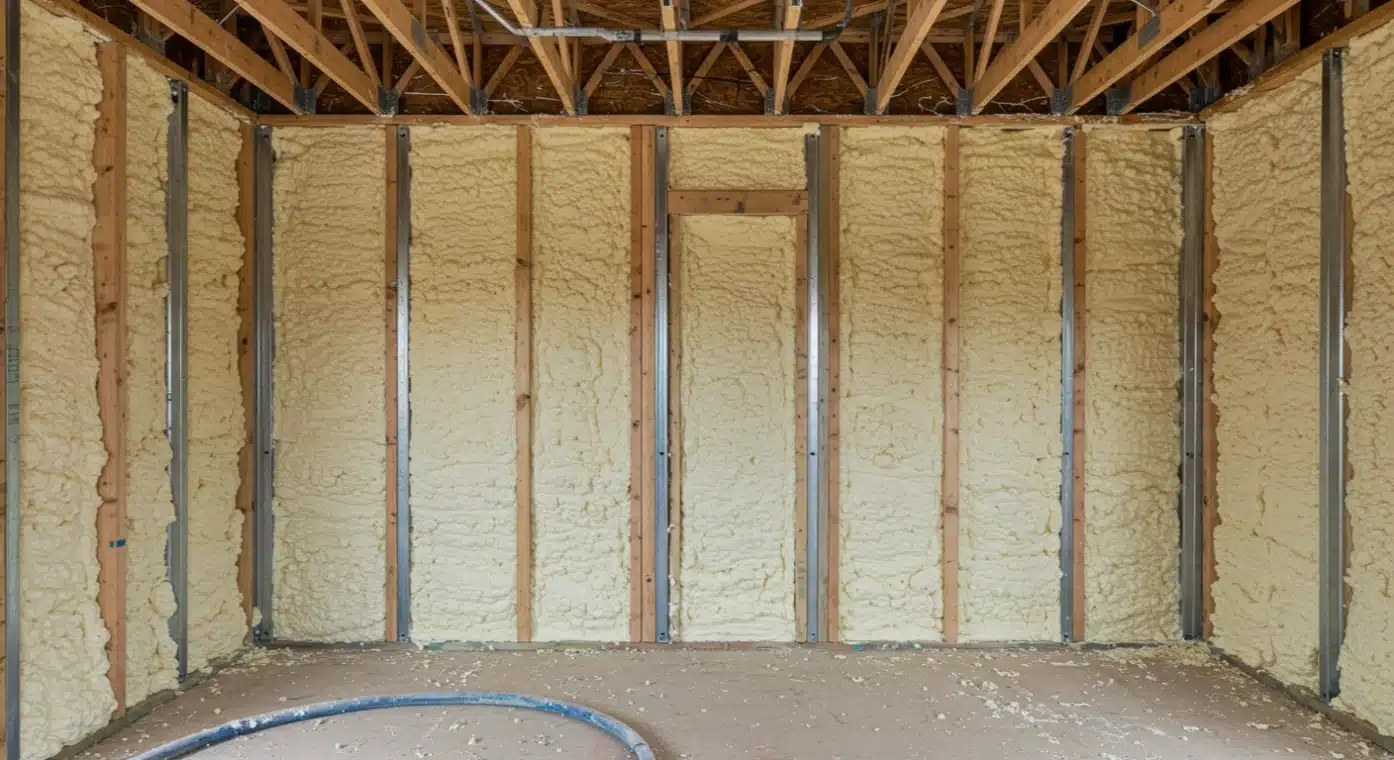
Professional Services for Lemoore Homeowners
- Attic Insulation Services: Complete attic sealing and insulation using spray foam to eliminate stack effect drafts and improve thermal performance throughout the home.
- Crawl Space Insulation: Comprehensive crawl space encapsulation that prevents ground moisture infiltration while eliminating drafts through floor systems.
- Spray Foam Repairs: Professional assessment and repair of existing insulation systems that have failed to maintain air sealing performance.
- Commercial Building Applications: Large-scale spray foam installation for commercial structures requiring superior air sealing and thermal performance.
Things to Consider Before Installation
Evaluate your home’s existing ventilation system before spray foam installation. Comprehensive air sealing may require mechanical ventilation upgrades to maintain indoor air quality. Professional assessment ensures proper ventilation balance after eliminating uncontrolled air leakage.
Consider the specific areas where drafts are most problematic. Targeted application in high-priority zones may provide significant improvement at lower cost than whole-house treatment. Professional thermal imaging can identify the most critical areas requiring attention.
Understand the difference between open and closed cell applications for your specific situation. Closed cell foam provides superior air sealing but costs more, while open cell foam offers good performance for interior applications at lower material cost.
Bonus Tip: Document existing comfort issues and energy bills before installation to accurately measure improvement after spray foam application.
Key Considerations for Long-term Performance
Understanding spray foam’s permanent nature is crucial for homeowners. Unlike traditional insulation materials that can be easily removed or replaced, spray foam creates a permanent bond with building materials. This permanence provides long-term performance benefits but requires careful consideration of future renovation plans.
Professional installation ensures optimal performance and prevents common issues such as over-expansion, incomplete coverage, or application in unsuitable conditions. The investment in professional installation pays dividends through consistent long-term performance and energy savings.
The material’s ability to maintain its cellular structure and air sealing properties over decades makes it particularly valuable in Lemoore’s climate, where temperature extremes can cause other insulation materials to settle, shift, or lose effectiveness over time.
Get Professional Draft Elimination Solutions
Addressing drafty home problems requires professional assessment and proper material selection for your specific situation. Supreme Spray Foam Fresno brings extensive experience in Central Valley climate challenges and proven solutions for eliminating uncomfortable drafts while improving energy efficiency.
Professional installation ensures optimal performance and long-term satisfaction with your investment. Contact Supreme Spray Foam Fresno at (559) 545-0800 or email [email protected] to schedule a comprehensive assessment of your home’s air sealing needs and discuss the most effective spray foam solution for your specific situation.
Common Questions About Draft Elimination
How quickly will I notice draft elimination after installation?
Air sealing benefits are immediately noticeable, with complete temperature stabilization typically achieved within 24-48 hours after installation.
Can spray foam installation address all draft sources?
Professional installation addresses 90-95% of air leakage sources, with remaining issues typically related to windows, doors, or structural settling that requires separate attention.
What maintenance is required after installation?
Properly installed spray foam requires no maintenance and maintains its air sealing properties for decades without degradation.
Will spray foam installation affect my home’s resale value?
Energy efficiency improvements through comprehensive air sealing typically increase home value and appeal to buyers concerned about utility costs.